
Use our branch locator to discover where we are. We can deliver your chosen items, supplies, and building materials right to your site, or, if you prefer, you can collect them from your nearest branch. Or how about our selection of aerated concrete aircrete blocks? Both strong and versatile, water and frost resistant, these blocks can be used across your build, for outward-facing brick walls, separating walls, foundations and much more. We have concrete blocks perfect for building an external wall, as well as foundation blocks, cavity walls, load-bearing walls, block flooring and an array of other internal and external applications. With branches across the South West of England, you can add convenience to peace of mind in knowing we only supply the very best products. When it comes to all your builds and renovations, you need a builders' merchants you can trust and that's exactly what you will find here at RGB. If your next building project requires dense concrete blocks, make sure to browse the products listed above and click the links to find out more. Whether you require an aircrete block or a high strength block, our selection will ensure your job is completed to the highest standard. Or during hardening, the temperature and pressure must be adjusted correctly so that the strength of the block can be high.We have a wide range of concrete blocks in a variety of sizes to suit your needs. For example, as blocks come out of the machine, their dimensions should be checked by means of laser sensors. Meticulous care should be taken from the mixing stage to the storage stage. In order for concrete blocks to be products that comply with the standards, they should be checked frequently during manufacturing. The blocks are turned into three large blocks, which are three or four blocks high and six blocks wide, and moved to the warehouse.Cured concrete blocks are removed with shelves from the oven.

Here, the blocks are baked with low pressure steam or in a high pressure steam oven called an autoclave. The hardening furnace is in the form of a chamber with a width that can fit more than one shelf at a time.After each shelf is filled, it is transported to the hardening furnace. The pallets loaded with blocks are transferred to the stacker and from there to the curing rack.The compressed blocks are pushed out with a pallet.When the molds are completely filled, they are compressed with the upper mold head and hydraulic system.The machine pushes the fluid concrete into the molds at the bottom. Concrete passes into another chamber on the block machine.It is poured into the conveyor after mixing.At this stage, colorants and chemicals can be added. If the plant is in a hot area, the temperature of the water should be adjusted carefully.
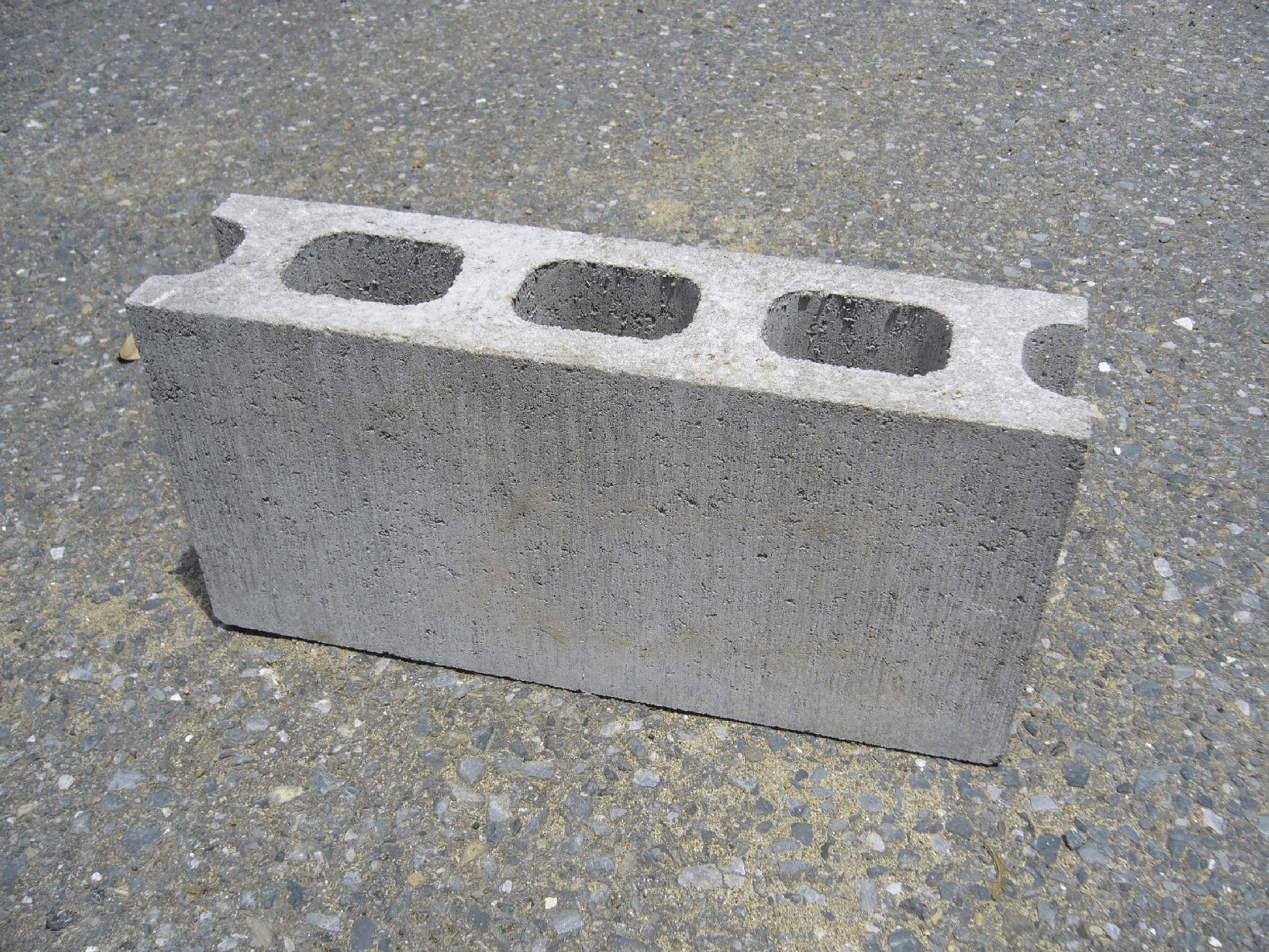

In addition to the basic materials, some chemicals can be added during concrete block making. Lightweight concrete blocks can be made with pumice. These blocks are used for walls that do not carry much load. The average weight of these blocks is 10.0 – 12.7 kg. In these, expansive clay is used instead of sand and gravel. While the average weight of a typical concrete block is between 17.2 and 19.5 kg, the weight of a slag block is between 11.8 and 15.0 kg.Īnother type of block is lightweight concrete blocks. The blocks generated right are called slag blocks. Granulated coal or slag can be used instead of sand and gravel in concrete block making.
Concrete blocks how to#
How To Make Concrete Blocks ? Which Process Is Followed ?
